In glass manufacturing, air-regenerative furnaces consume the largest amount of resources in the process, and they also are the source of the highest emissions. For more than three decades, manufacturers have understood that oxy-fuel combustion reduces energy consumption, emissions and carbon footprint. However, converting an existing system to an oxygen-fired system is a costly capital investment with a slow return on investment (ROI) that has kept many glass manufacturers from making the switch.
However, a new technology solution provides a cost-effective means to enable manufacturers to transform their processes and make a positive impact. The OPTIMELT
® Thermo Chemical Regenerator (TCR) technology, developed by Linde, provides the cost-savings boost needed to make the investment viable.
U.S. Borax has been a partner of the glass industry for many decades. Boron, essential in the formulation of many glass applications, aids the
glass manufacturing process, acting as both a flux and network former and lowering melting temperature. Recognizing our extensive chemical and industry expertise, Linde included U.S. Borax scientists in its rigorous and extended testing of OPTIMELT TCR technology in borosilicate glass manufacturing facilities.
What producers would benefit most from inclusion of OPTIMELT TCR?
OPTIMELT TCR technology may help borosilicate glass producers who:
- Have a large-volume furnace pull
- Need to meet tight NOx regulations
- Are sensitive to energy costs
- Operate with a high furnace temperature
- Are interested in switching from air fuel to oxy fuel
- Have a tight space for retrofit
- Need to increase specific pull of the furnace
Testing OPTIMELT TCR: U.S. Borax expertise and partnership
U.S. Borax partnered with Linde and glass production optimization experts at CelSian, through bench scale tests and pilot scale tests—contributing financial input and boron product knowledge to the project.
Given the evaporation characteristics of boron in batch formulation and in furnace operations, it was important to address concerns about deposit accumulation in borosilicate glass furnaces. When using OPTIMELT TCR technology for their borosilicate glass formulations, would manufacturers face the same maintenance issues they do with legacy air-regenerative furnace technology?
The answer from the joint-project is no. The project outcomes clearly demonstrated that boron species are not deposited, and no accumulation is present in the OPTIMELT thermochemical regenerators.
Answering questions like this one is an essential role of U.S. Borax. Our customer-centric focus in product development and support has led us to become leaders in borate research—and in research into solutions for the industries that use borates.
This partnership approach brings value to all participants, supporting the movement toward more environmentally sustainable solutions in industry and across society. Through collaboration and pioneering innovations, U.S. Borax supports the spirit of
Rio Tinto’s sustainability commitment.
Increasing fuel efficiency in glass manufacturing
OPTIMELT TCR recovers waste energy stored in regenerator checkers by preheating the fuel and endothermically reacting the fuel with the carbon dioxide (CO
2) and water (H
2O) in recycled flue gas. The endothermic reforming reaction converts the fuel to hot syngas
, which is combusted with oxygen in the furnace.
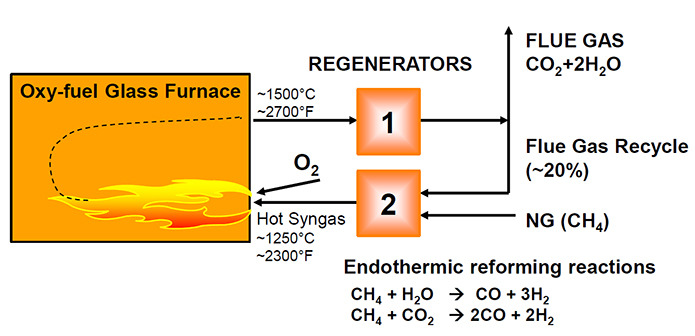
Reforming natural gas in regenerators in this way recovers twice as much heat from the flue gas in oxy fuel furnaces as simply preheating the combustion air.
The result? Net fuel consumption is reduced by 20-30%.
OPTIMELT TCR: Reduce operating expenses, improve productivity
In addition to maximizing fuel efficiency, OPTIMELT TCR technology provides extended benefits that can help glass manufacturers improve the profitability of their operations. In testing over multiple years in commercial pilots, U.S. Borax and CelSian scientists documented cleaner operations, reduced emissions, and an increased pull rate for the glass itself.
Self-cleaning checker stack
In conventional air regenerators, alkali vapors in flue gas react with sodium, oxygen, and borates to form salt deposits that build up inside the checker channels. These deposits reduce the regenerator’s efficiency and increase fuel consumption. Handling the issues requires periodically shutting down and cleaning the furnaces—an increased maintenance cost.
In the commercial demonstration systems of OPTIMELT TCR regenerators,
no deposit accumulation occurred. Checker channels remained clean, even after two and a half years of operation.
Laboratory tests revealed the reason for the cleaner operation: The evaporation rate of sodium salts exceeds the deposition rate. Sodium deposited on the regenerators during the flue gas cycle evaporate during the syngas cycle, thus leaving the checker channels clean. Likewise, boron evaporation rate exceeds deposition rate. Hence,
there are virtually no borate deposits in the system.
The efficiency of the syngas burn—results in cleaner burning. In the commercial systems,
NOx emissions were reduced 80% compared to conventional oxy-fuel burners. The syngas flame resulted in a substantial reduction in foam levels relative to conventional oxy-fuel furnaces.
Maintaining uniform temperature
Computational fluid dynamics (CFD) models show that in conventional oxy-fuel systems, glass surface temperatures vary greatly inside the furnace. The need to accommodate those temperature differences limits glass pull rate and overall productivity of the operation.
However, the OPTIMELT TCR system’s efficiency and method of recirculation also enable a more uniform temperature distribution that allows for , an increased pull rate while staying within crown temperature limits. In addition, glass quality and color are improved.
Cost-effective retrofit with attractive benefits
Glass manufacturers now have an option that not only reduces their NOx emissions and carbon footprint but also improves productivity and profitability. Combining fuel savings with measurable operational boosts—and significant maintenance cost reductions—provides an attractive rationale for moving to OPTIMELT TCR technology.
U.S. Borax is committed to continued partnership with Linde for upcoming commercial demonstration implementations. We look forward to exploring how our borosilicate customers and partners can benefit from this technology.
Want to learn more? Visit Linde’s web site:
https://www.lindeus.com/industries/glass/optimelt
Resources