This article originally appeared in the November/December 2020 issue of Glass Worldwide Magazine. Reprinted with permission.
In the case of sodium tetraborate (commonly used in borosilicate glass or C-glass fiber applications), hydrous refers to Na
2B
4O
7·5H
2O whereas anhydrous refers to Na
2B
4O
7. In other words, anhydrous boron is a more concentrated form of boron—containing 1.4 times more B
2O
3. The additional value that anhydrous products bring goes beyond the concentration difference of B
2O
3.
Higher chemical concentration helps with debottlenecking the pull capacity and logistic/materials handling costs. The lack of crystal water in anhydrous and the absence of puffing and decrepitation phenomena are fundamental to other volatility related benefits.
Learn more about some of these benefits:
Energy savings
An anhydrous product, such as
Dehybor®, will use less energy to melt than a hydrous product, such as
Neobor®. The actual savings will depend upon the energy source and plant condition.
Figure 1: Energy necessary to melt borate products.
From a theoretical calculation, using anhydrous batch will enable an energy reduction of approximately 3%. Recent laboratory studies managed by CelSian and done within the framework of a GlassTrend consortium project used a time-dependent batch energy measurement system. They showed that glass batch using anhydrous is able to achieve more than 11% in energy savings, which is consistent with typical C-glass producer feedback.
Figure 2: Graph courtesy of CelSian. Used with permission.
Energy savings are an important consideration for C-glass manufacturers located in countries where gas prices are relatively high. Apart from gas price, savings will also be subject to plant specific variables, such as the amount of cullet used and the choice of raw materials. With less volatility loss of B
2O
3 , the
Dehybor batch will further enhance the energy savings.
Improved productivity
Apart from a higher concentration in B
2O
3, anhydrous products also have a higher bulk density so anhydrous batch will create more space for other raw materials—de-bottlenecking capacity when pull is constrained. Typically, AB-consuming C-glass producers have reported a 3% capacity gain when using an anhydrous product. Although the extent of gains are subject to batch formulation and other process constraints, improved productivity is usually considered the most significant component of the value-in-use of anhydrous products. This provides not only a long-term benefit but also flexible short-term alternative to capital investment.
Reduced volatility loss
Boron is volatile and subject to loss through emissions. High emissions could mean:
- Loss of raw materials and the expense that incurs
- Additional cost involved with handling dust captured by the abatement system, if available
- Environmental compliance pressure
- Process challenge
An anhydrous product will improve volatility reducing boron loss through emissions. In part, the significant differences in behavior are attributed to puffing and decrepitation phenomena of
Neobor when releasing water from the crystal structure. The observation can be replicated in high temperature observation camera systems that record the height and condition of batch at different time and temperature intervals.
Figure 3
Typical emission loss of B
2O
3 in the
Dehybor batch and the
Neobor batch are 5% and 10% respectively. In some Asian C-glass producing plants, where the emission loss of using
Neobor is more severe than 10%, hydrous products provide an attractive solution.
Reduced erosion to the furnace
While it is hard to quantify in the short-term, reduction of boron and sodium volatility will then, in theory, improve corrosion resistance of a furnace, and lower the lifetime maintenance costs.
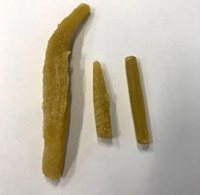
One qualitative case study: A C-glass producer collected wall deposition during a furnace cold-repair and sent them to U.S. Borax for testing. Our lab identified high Al
2O
3 and high B
2O
3. According to the manufacturer, the elevated Al
2O
3 level was believed to be from the furnace’s high-Al bricks. After switching to an anhydrous borate product
, the company found that the occurrence of wall deposition had been reduced.
Figure 4
Composition |
SiO2 |
Al2O3 |
Na2O |
B2O3 |
Content |
17.7% |
23.2% |
15.8% |
31.8% |
Reduced freight cost and end product quality
Because of its higher concentration, anhydrous products translate into freight benefits. Furthermore, although sporadically and less commonly mentioned, some manufacturers commented that anhydrous batch helps the application and process control of cullet containing melt.
Future work and limitations
Despite of all of the significant benefits of using
Dehybor, some C-glass producers have suggested that it cannot be used in cold-top electric furnaces due to earlier occurrences of volcano with
Dehybor batch. U.S. Borax is researching the boundary and enablers of anhydrous products in this furnace type.
Keep in mind that the applicability and the extent of each benefit are subject to plant conditions and may vary in real-world applications.
U.S. Borax’s technical service team works with customers to explore and verify these benefits through controlled plant trials. Our technical service team can also provide other value-added services, including defect analysis and raw materials analysis.
Resources